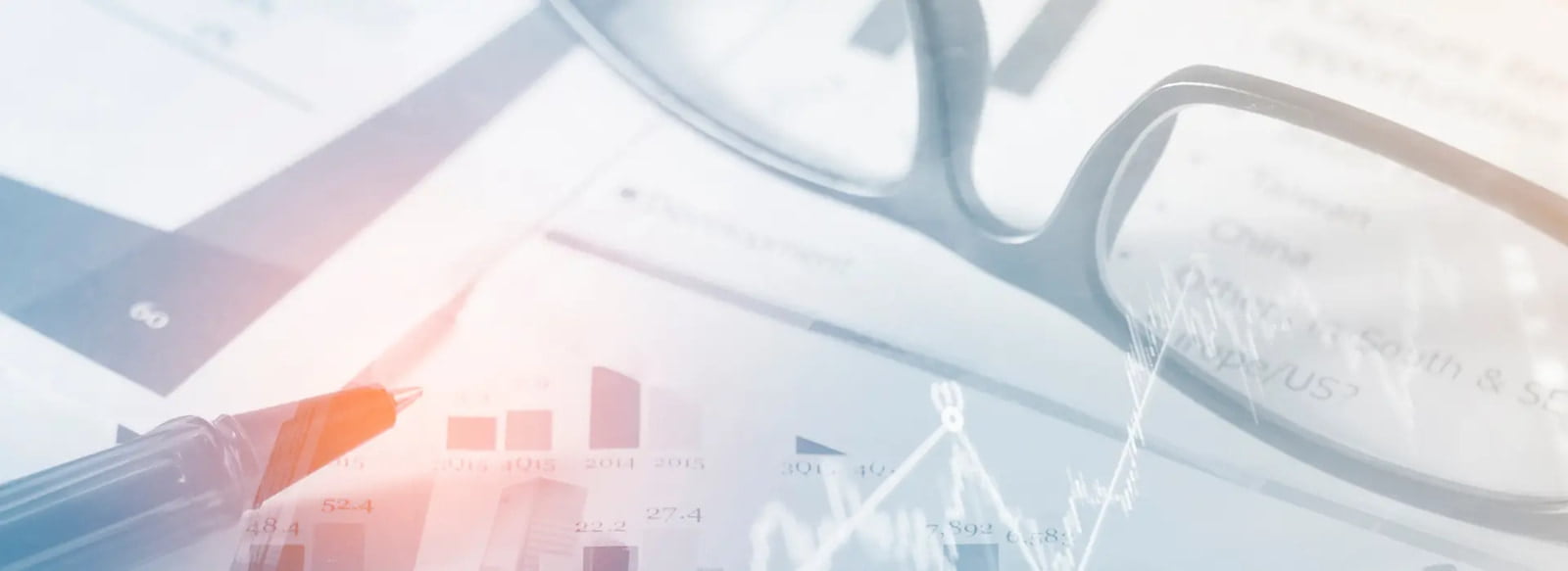
Introduction to Lean
Introduction to Lean
Lean is a systematic approach to enhancing efficiency and eliminating waste in business processes. Originating from manufacturing, Lean principles have expanded to various industries, promoting a culture of continuous improvement and value creation. This article delves into the foundations, principles, and practical applications of Lean, providing a comprehensive understanding of this powerful philosophy.
Lean Foundation
Lean Foundation
The underlying foundation of Lean is encapsulated in the PDCA cycle—Plan, Do, Check, Act. This continuous improvement process aligns with Lean's focus on creating value and eliminating waste. The cycle encourages businesses to constantly evaluate and refine their processes to achieve optimal efficiency and quality.
The PDCA Cycle
The PDCA Cycle
- Plan:
- Identify and Analyse the Problem: Start by identifying a specific process or problem area that needs improvement.
- Set Objectives: Define clear objectives aligned with Lean’s focus on delivering value.
- Develop a Plan: Create a detailed action plan for improvement, mapping the current state of a process, identifying waste (non-value-added activities), and proposing changes to eliminate this waste.
- Do:
- Implement the Plan: Put the plan into action on a small scale, experimenting with changes that can reduce waste and increase efficiency.
- Apply Lean Tools: Utilise Lean tools like 5S, Kaizen, or Kanban to streamline processes and make the workflow more efficient.
- Check:
- Monitor and Measure: Collect data and measure the outcomes of the changes made, assessing whether the changes are moving towards the set objectives.
- Analyse Results: Compare the results against the expected outcomes, examining how the changes have impacted efficiency, quality, and time taken in the process.
- Act:
- Standardise Successful Changes: If the results are positive, implement the changes on a larger scale and standardise the new, more efficient processes across the organisation.
- Identify Further Improvements: If the objectives weren’t fully met, identify what didn’t work and why, using these insights to start a new PDCA cycle and refining the approach for better results.
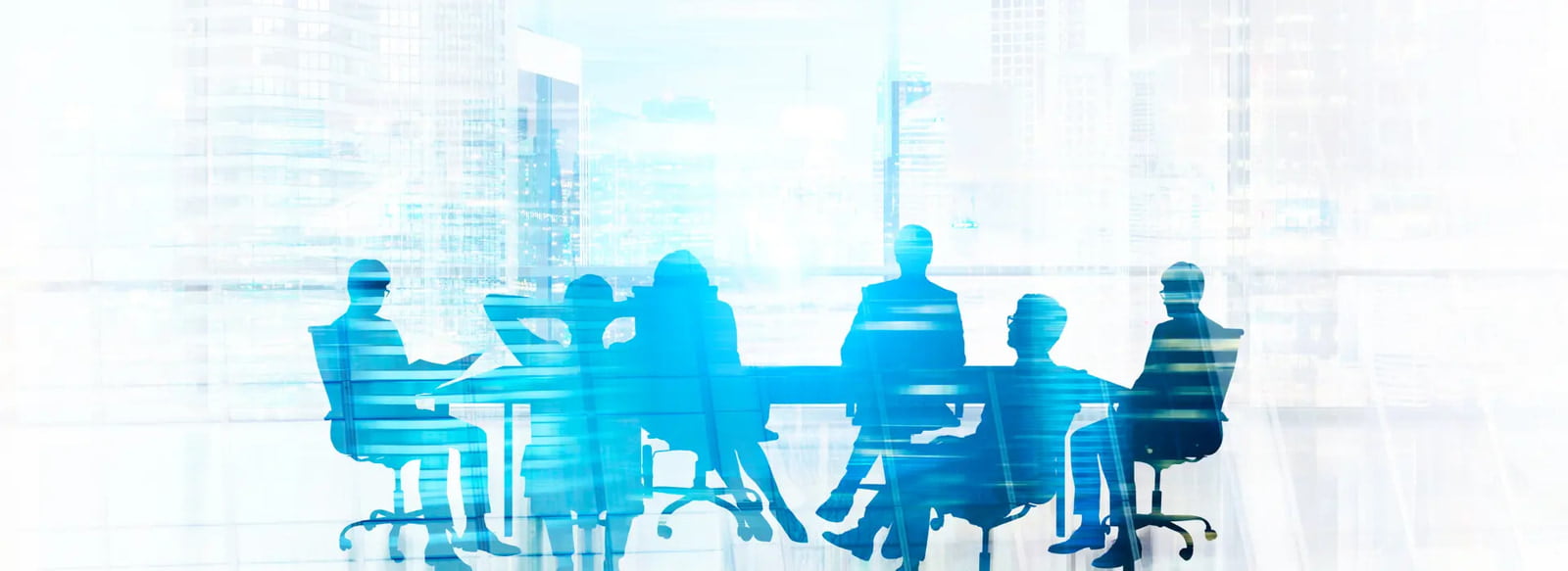
History of Lean
History of Lean
Lean’s origins can be traced back to the early 1900s with Henry Ford's assembly line innovations. In the 1940s and 1950s, the Toyota Production System (TPS) was developed by Taiichi Ohno and others at Toyota, integrating concepts of just-in-time production and Jidoka (automation with a human touch). By the 1970s and 1980s, Western businesses, especially in the automotive sector, began adopting these methods. The term "Lean" was popularised in the 1990s by the book "The Machine That Changed the World" by James P. Womack, Daniel T. Jones, and Daniel Roos. Since the 2000s, Lean principles have expanded beyond manufacturing to sectors like healthcare, software, and services, focusing on customer value, waste reduction, and continuous improvement.
Lean Principles
Lean Principles
Lean principles are fundamental guidelines that drive the Lean philosophy. They focus on delivering value to the customer while minimising waste. There are five core Lean principles:
- Value:
- Define value from the customer's perspective.
- Understand what the customer really needs and is willing to pay for.
- Value Stream:
- Identify the value stream for each product or service, mapping all the steps required from concept to delivery.
- This process helps in identifying and eliminating waste.
- Flow:
- Make the value-creating steps occur in a tight sequence so the product or service flows smoothly towards the customer.
- Ensure that work processes are streamlined and uninterrupted.
- Pull:
- Instead of pushing products to the market, let customer demand pull them through the production process.
- This approach helps in reducing overproduction and inventory.
- Pursuit of Perfection:
- Continuously pursue perfection by constantly improving the value stream.
- Aim to provide the highest quality products and services with zero waste, fostering a culture of continuous improvement.
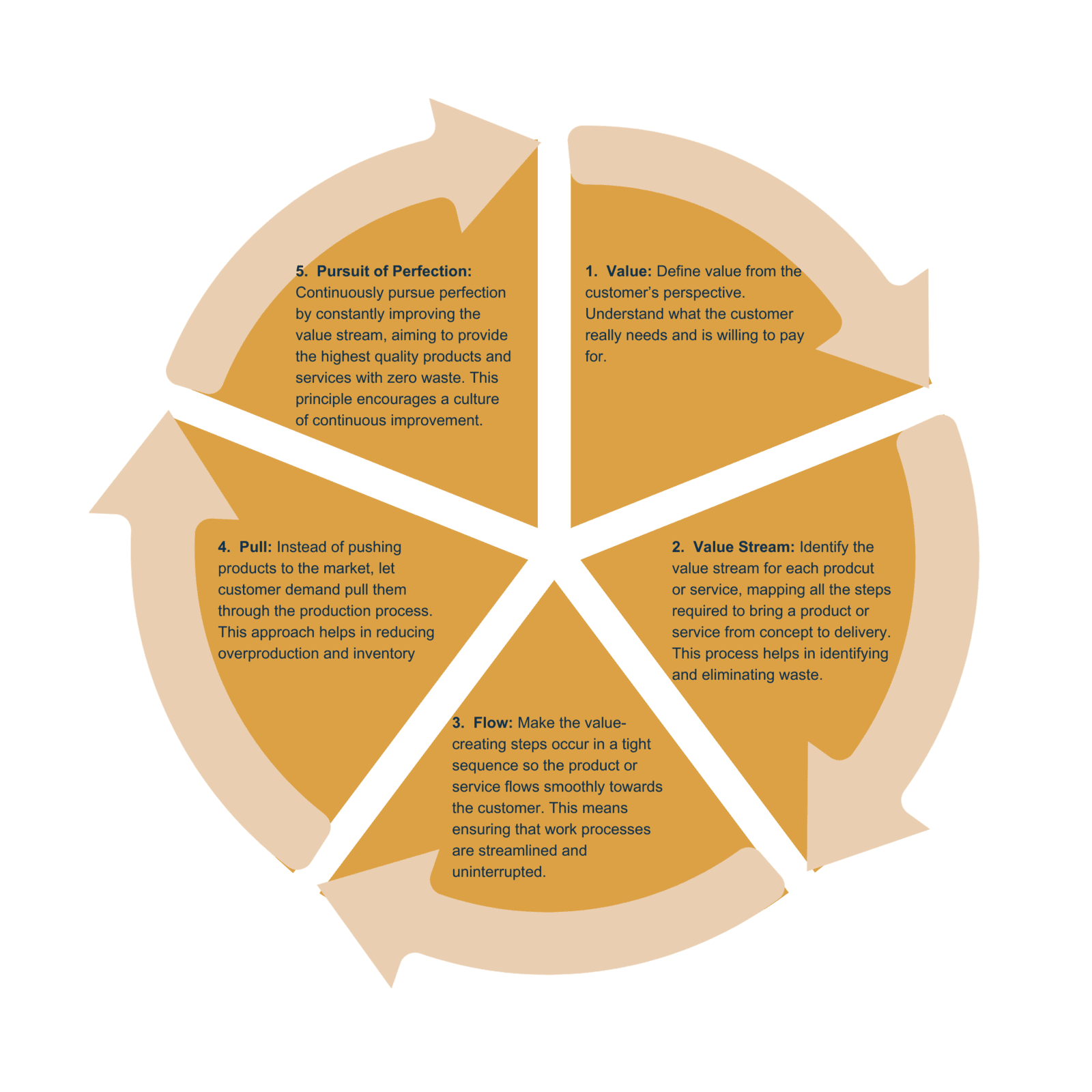
Principle 1: Value
Principle 1: Value
Value is defined from the customer's perspective. Understanding what the customer needs and is willing to pay for is crucial. Customers consider various factors when defining value, such as:
- Quality of the product or service.
- Price compared to competitors' products.
- Speed of delivery.
- Experience of purchasing.
- Customer service.
- Visual aesthetics.
- Convenience of use.
Principle 2: Value Stream
Principle 2: Value Stream
A value stream encompasses the entire set of activities or processes that add value to a product or service from creation to delivery. This concept is essential in Lean management systems and thinking, focusing on optimising efficiency and quality.
Identifying Waste
Identifying Waste
In Lean, waste is any activity or process that does not add value to the customer. The eight types of waste (DOWNTIME) are:
- Defects: Products or services that are out of specification and require additional resources to correct.
- Overproduction: Producing more than what is needed or before it is needed.
- Waiting: Idle time when resources are not being used effectively.
- Non-utilised Talent: Underutilising people’s skills, talents, and knowledge.
- Transport: Unnecessary movements of products or materials.
- Inventory Excess: Holding more materials, parts, or products in stock than needed.
- Motion: Unnecessary movements by people.
- Extra-Processing: Doing more work or using more resources than necessary.
Principle 3: Flow
Principle 3: Flow
Flow ensures that value-creating steps occur in a tight sequence, allowing products or services to move smoothly towards the customer. This principle focuses on minimising waiting and delays, eliminating bottlenecks, optimising physical layouts, ensuring quality at each step, and simplifying and standardising work.
Principle 4: Pull
Principle 4: Pull
The pull principle involves producing products based on actual customer demand rather than forecasted demand. This approach reduces overproduction and inventory, ensuring that resources are used efficiently. A pull system aligns production closely with customer preferences and market trends.
Principle 5: Pursuit of Perfection
Principle 5: Pursuit of Perfection
The pursuit of perfection involves continuously improving the value stream to provide the highest quality products and services with zero waste. This principle fosters a culture of continuous improvement, where mistakes and inefficiencies are seen as opportunities for learning and improvement. Employees are trained and empowered to identify waste and inefficiencies, and everyone is encouraged to contribute ideas for improvement.
Benefits of Lean to a Business
Benefits of Lean to a Business
Implementing Lean principles offers numerous benefits to businesses:
- Increased Efficiency: By eliminating waste in processes, Lean helps streamline operations, leading to higher efficiency.
- Cost Reduction: Focusing on eliminating non-value-adding activities reduces costs in production, inventory management, and labor.
- Improved Quality: Lean emphasises continuous improvement and defect prevention, leading to higher quality products and services.
- Customer Satisfaction: Focusing on customer value enhances satisfaction and loyalty.
- Employee Engagement and Empowerment: Lean encourages a culture of problem-solving and improvement, leading to higher employee engagement and job satisfaction.
- Faster Delivery Times: Streamlined processes and reduced waste lead to shorter production cycles and faster delivery times.
- Cultural Transformation: Lean implementation leads to a cultural shift towards continuous improvement and proactive problem-solving.
- Better Resource Utilisation: Lean optimises the use of resources, ensuring materials, labor, and capital are used effectively.
- Competitive Advantage: Improved efficiency, quality, and customer satisfaction provide a significant competitive edge.
Lean Framework for Implementation
Lean Framework for Implementation
To successfully implement Lean, organisations can follow a structured framework that includes Lean leader philosophy, Lean management systems, and Lean operating systems tools.
Lean Leader Philosophy (Guiding Principles And Mindset):
Lean Leader Philosophy (Guiding Principles And Mindset):
- 5 Lean Principles: Steps to improve processes: define value, map steps, create flow, pull from customer demand, and seek perfection.
- Systems Design: Organise processes efficiently to work smoothly and reduce waste.
- Waste Elimination: Remove unnecessary steps to make processes faster and cheaper.
- Value for the Customer: Focus on giving customers exactly what they need, when they need it.
- People Development: Train and empower employees to keep improving their work.
- PDCA (Plan-Do-Check-Act): A cycle for trying out changes, checking results, and making improvements continuously.
Lean Management Systems (Framework For Implementation):
Lean Management Systems (Framework For Implementation):
- A3 Problem Solving: A structured problem-solving approach that helps identify root causes and implement effective solutions.
- Value Stream Management: Optimising the value stream to align with long-term business goals and responding to changing customer demand.
- Leader Standard Work: Establishing standard routines for leaders to support Lean implementation.
- Going to the Gemba: Leaders visiting the workplace to observe and understand processes.
- Heijunka: Production levelling to smooth out fluctuations in demand.
- Visual Controls: Using visual tools to monitor processes and performance.
Lean Operating Systems Tools (Tools Used On The Ground):
Lean Operating Systems Tools (Tools Used On The Ground):
- Kaizen: Continuous improvement initiatives that involve all employees.
- Value Stream Mapping: Mapping processes to identify and eliminate waste.
- Standard Operating Procedures (SOPs): Documenting standard processes to ensure consistency and efficiency.
- Kanban and Pull Systems: Implementing pull systems to align production with customer demand.
- 5S: A workplace organization method that enhances efficiency and safety.
- Cell Design: Arranging workstations to optimize flow and reduce waste.
- Poka-Yoke: Error-proofing techniques to prevent defects.
Conclusion
Conclusion
Lean is a powerful philosophy that drives continuous improvement, efficiency, and value creation. By understanding and applying Lean principles, businesses can eliminate waste, enhance quality, and deliver greater value to customers. The journey to Lean involves a commitment to continuous learning and improvement, fostering a culture that embraces change and innovation. By adopting Lean, organisations can achieve significant benefits, including increased efficiency, cost reduction, improved quality, customer satisfaction, employee engagement, and a competitive advantage in the market.