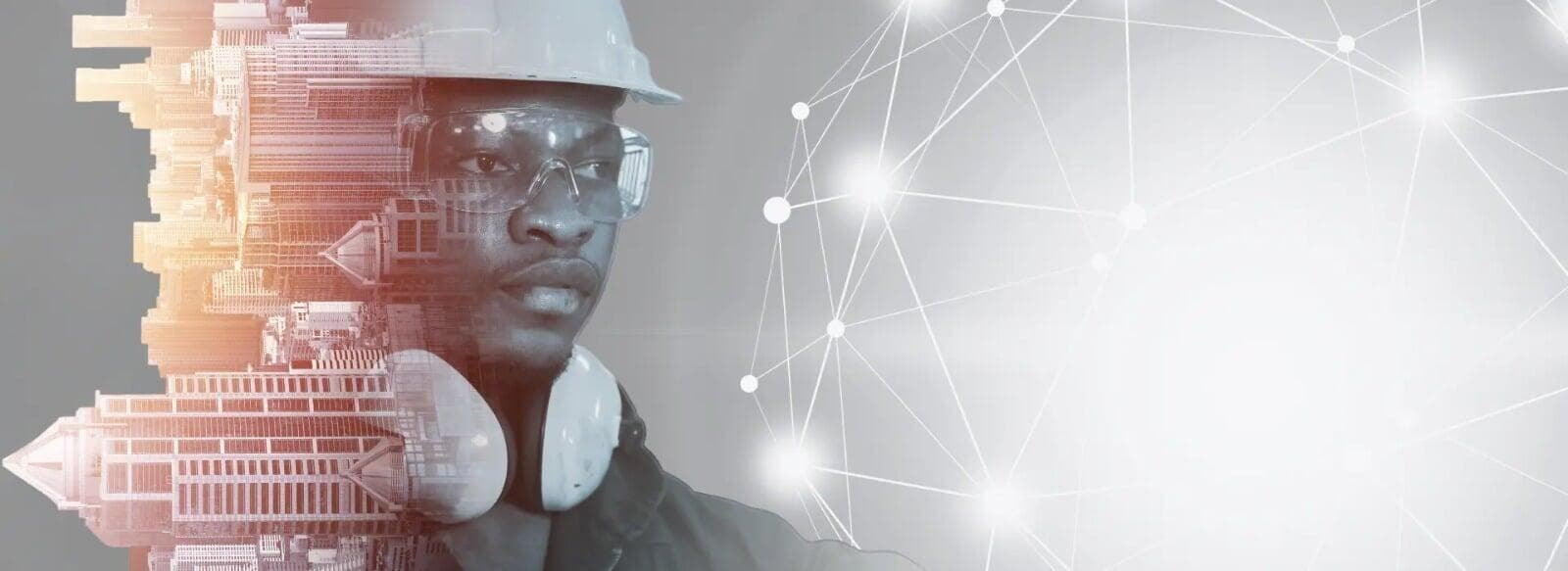
Why Lean Thrives in Real-World Applications
In the modern business environment, where speed and adaptability often determine success, Lean methodology shines as an essential framework.
Rooted in principles of continuous improvement and waste reduction, Lean offers an unparalleled advantage: it can be deployed immediately. By focusing on "learning by doing," Lean enables companies to bypass the lengthy theoretical onboarding typically required by other frameworks, allowing employees to engage with Lean practices directly in their day-to-day tasks.
This pragmatic, action-first approach doesn’t just streamline workflows—it builds an organizational culture of engagement, empowerment, and innovation. From overcoming resistance to Lean adoption to scaling it enterprise-wide and initiating cultural transformation, this article explores how Lean delivers results from day one. We’ll also outline how organizations can get started within hours and sustain Lean’s momentum over the long term.
1. Challenges in Traditional Skill Development
1. Challenges in Traditional Skill Development
The Inefficiencies of Theoretical Learning
For decades, organizations have relied on training models that emphasize theory over practice. While these methods have merits, they introduce several inefficiencies:
- Lengthy Onboarding Periods: Employees are often required to undergo weeks or months of classroom-style training before applying their skills.
- Knowledge Decay: Without immediate application, concepts learned in isolation are forgotten or misunderstood.
- High Costs and Logistics: The resources spent on trainers, materials, and time away from core tasks can add significant overhead.
These challenges create a gap between learning and implementation, leading to delayed improvements, employee frustration, and inefficiencies.
Lean’s Pragmatic Approach: Immediate Learning, Immediate Results
Lean flips traditional learning on its head. Its foundational tools and principles allow employees to learn by engaging directly with their work:
- 5S (Sort, Set in Order, Shine, Standardize, Sustain): Teams transform their workspaces into efficient, clutter-free environments in a single day, seeing immediate benefits.
- Gemba Walks: Leaders and employees observe actual work processes, fostering insights into inefficiencies and opportunities for improvement.
- Value Stream Mapping: Teams visually map workflows to identify bottlenecks and prioritize value-adding activities.
By combining theory with hands-on application, Lean eliminates the delays and inefficiencies associated with traditional skill acquisition.
2. The Cultural Shift of Learning by Doing
2. The Cultural Shift of Learning by Doing
Building a Continuous Improvement Culture
The "Learn by Doing" approach doesn’t just accelerate skill acquisition—it fosters a culture of engagement, accountability, and innovation. Here’s how:
- Empower Employees: When employees are actively involved in problem-solving, they feel a sense of ownership over the outcomes. This empowerment drives engagement and motivation.
- Break Down Silos: Lean encourages cross-functional collaboration. Teams work together to identify inefficiencies and implement solutions, fostering a culture of teamwork.
- Encourage Experimentation: With its emphasis on small, incremental changes, Lean creates a safe environment for experimentation. Employees learn that mistakes are opportunities for growth, not failures.
- Focus on Value: By consistently prioritizing customer value, Lean aligns everyone’s efforts toward a common goal.
This shift in mindset transforms Lean from a methodology into a shared organizational philosophy. It cultivates an environment where continuous improvement becomes second nature, and everyone contributes to achieving operational excellence.
The Long-Term Benefits of a Lean Culture
Organizations that embed Lean into their culture experience transformative benefits:
- Higher Employee Engagement: Hands-on involvement in Lean initiatives boosts morale and reduces turnover.
- Enhanced Customer Satisfaction: Continuous improvement ensures that processes are aligned with customer needs, resulting in better products and services.
- Greater Resilience: Lean organizations are better equipped to adapt to disruptions and seize new opportunities.
3. How to Get Started with Lean in a Few Hours
3. How to Get Started with Lean in a Few Hours
The First Steps Toward Lean Transformation
Lean’s simplicity makes it easy to begin. Here’s a step-by-step guide to starting Lean in just a few hours:
- Educate Your Team: Host a short workshop or meeting to introduce Lean’s principles, tools, and benefits.
- Select a Pilot Process: Focus on a workflow with clear inefficiencies and measurable outcomes.
- Engage Employees Immediately: Use a Gemba walk or Value Stream Mapping session to involve employees in identifying challenges.
- Apply Simple Lean Tools: Start with foundational practices like 5S or Kanban boards to generate immediate improvements.
- Set Clear Metrics: Define success metrics to track progress and demonstrate Lean’s value to stakeholders.
Achieving Quick Wins
Within hours, Lean can deliver tangible results:
- Improved Workspaces: 5S practices declutter and optimize environments for better productivity.
- Streamlined Processes: Value Stream Mapping uncovers bottlenecks and creates actionable improvement plans.
- Aligned Teams: Kanban boards enhance visibility and coordination across workflows.
These quick wins build momentum, creating a strong foundation for expanding Lean practices.
4. Scaling Lean Across the Organization
4. Scaling Lean Across the Organization
From Localized Pilots to Enterprise-Wide Adoption
Scaling Lean effectively involves moving from isolated projects to a fully integrated organizational framework:
- Start Small: Begin with a specific process, department, or team. Focus on areas where inefficiencies are visible and improvements can be easily measured.
- Standardize Practices: Develop templates and guidelines for Lean tools to ensure consistency. Standardization simplifies implementation and ensures that successes can be replicated across departments.
- Expand Cross-Functional Collaboration: Lean thrives when departments work together. Use tools like Value Stream Mapping to address inefficiencies that span multiple areas of the business.
- Train Lean Champions: Identify employees who are passionate about Lean and train them to lead initiatives across the organization. These champions act as ambassadors, spreading the philosophy and supporting teams in their Lean journeys.
- Integrate Technology: Use software solutions to track Lean metrics, visualize value streams, and manage workflows. Digital tools can amplify the impact of Lean by providing real-time insights and data-driven decision-making.
- Continuously Improve: Lean is not a one-time project but a journey. Regularly revisit processes, gather feedback, and implement new improvements. By embedding Lean into the organization’s DNA, you create a sustainable culture of excellence.
Leveraging Technology for Seamless Scaling
Digital tools can accelerate Lean adoption across larger organizations:
- Kanban Boards: Visual systems streamline task management, enabling teams to prioritize work and minimize delays.
- Real-Time Dashboards: These provide visibility into Lean metrics, helping leaders track progress and identify bottlenecks.
- Automation and Data Integration: Automating repetitive tasks allows teams to focus on value-adding activities while maintaining data-driven decision-making.
Through a combination of strategic scaling and technological enablement, organizations can amplify Lean’s impact across all functions.
5. Sustaining Lean for the Long Term
5. Sustaining Lean for the Long Term
Continuous Improvement as a Core Value
Sustaining Lean requires organizations to view it as an ongoing journey rather than a one-time initiative. Key practices for long-term success include:
- Regular Kaizen Events: Frequent improvement sessions ensure that teams remain engaged and processes continue evolving.
- Leadership Commitment: Leaders should model Lean principles and actively participate in improvement efforts.
- Ongoing Training: Invest in professional development to deepen employees’ understanding of Lean tools and techniques.
Long-Term Outcomes
Organizations that sustain Lean achieve significant benefits:
- Operational Excellence: Lower costs, higher efficiency, and better resource utilization.
- Customer-Centric Innovation: Processes that consistently deliver value and exceed customer expectations.
- Scalable Growth: A culture of continuous improvement drives resilience and adaptability.
6. Overcoming Resistance to Lean Implementation
6. Overcoming Resistance to Lean Implementation
Sources of Resistance
- Fear of Job Cuts: Lean’s focus on efficiency can create anxiety among employees about potential downsizing.
- Misaligned Expectations: Managers may view Lean as a cost-cutting measure rather than a value-enhancing framework.
- Cultural Barriers: Established workflows and hierarchies often resist change, especially in traditional organizations.
- Lack of Trust: Previous experiences with failed improvement programs can foster skepticism about Lean’s promises.
Strategies to Address Resistance
Lean’s success depends on how organizations address these challenges. Proven strategies include:
- Transparent Communication: Clearly articulate Lean’s purpose—emphasizing its role in improving processes and empowering employees rather than reducing headcount.
- Involve Employees in Problem-Solving: Tools like A3 templates and Kaizen events encourage teams to contribute actively to solutions, fostering ownership and buy-in.
- Leadership Participation: Leaders must visibly support Lean by participating in Gemba walks, engaging in improvement events, and modelling desired behaviours.
- Showcase Quick Wins: Early successes—such as reducing waste or improving a workflow—build credibility and counter resistance.
- Continuous Engagement: Regular check-ins, workshops, and feedback loops help sustain momentum and reinforce commitment to Lean practices.
These strategies transform resistance into enthusiasm, setting the stage for successful Lean adoption.
Common objections include:
- "We’re too busy for this." Lean doesn’t require a significant time investment upfront. Starting small, with tools like 5S or a single Kaizen event, can yield quick wins without disrupting daily operations.
- "It’s too simplistic." While Lean tools are simple, their impact can be profound. The iterative nature of Lean ensures that even small changes lead to continuous improvement.
- "It won’t work in our industry." Lean principles are industry-agnostic. From manufacturing to healthcare, software to retail, Lean has been successfully implemented across diverse sectors.
Proactively addressing these objections with real-world examples and immediate results can ease skepticism and encourage broader adoption.
7. Success Stories: Lean in Action
7. Success Stories: Lean in Action
Example 1: Manufacturing Plant
A mid-sized manufacturing plant faced delays due to disorganized workstations. Within a single day, they applied the 5S methodology across the shop floor. Tools were sorted and labelled, equipment was cleaned, and workstations were reorganized. The result? A long term increase in efficiency and a noticeable boost in employee morale.
The success of this initial 5S implementation encouraged the company to expand Lean practices to other areas. Over time, they achieved significant cost savings and improved customer satisfaction.
Example 2: Healthcare Facility
A hospital struggling with patient wait times used Lean principles to map their patient intake process. A simple Kaizen event identified unnecessary steps and reallocated staff to high-demand areas. Within a week, patient wait times decreased, improving both patient satisfaction and staff efficiency.
This success prompted hospital management to integrate Lean training into their onboarding process, ensuring all new hires understood the principles of efficiency and waste reduction.
Example 3: Software Development Team
A software team implemented daily stand-up meetings and visual task boards (Kanban) to improve communication and workflow transparency. The immediate impact included fewer miscommunications, faster delivery times, and higher-quality output.
The team’s embrace of Lean principles inspired other departments to adopt similar practices, leading to company-wide improvements in efficiency and collaboration.
Conclusion
Conclusion
Lean’s "learn by doing" approach is more than a framework—it’s a transformative strategy that empowers organizations to achieve efficiency, adaptability, and innovation. By emphasizing immediate action, collaboration, and continuous improvement, Lean enables teams to deliver results from the start while fostering a culture of learning and growth.
For organizations seeking sustainable success, Lean provides a clear, actionable pathway. The journey begins not in theory but in practice—with the decision to take the first step today.