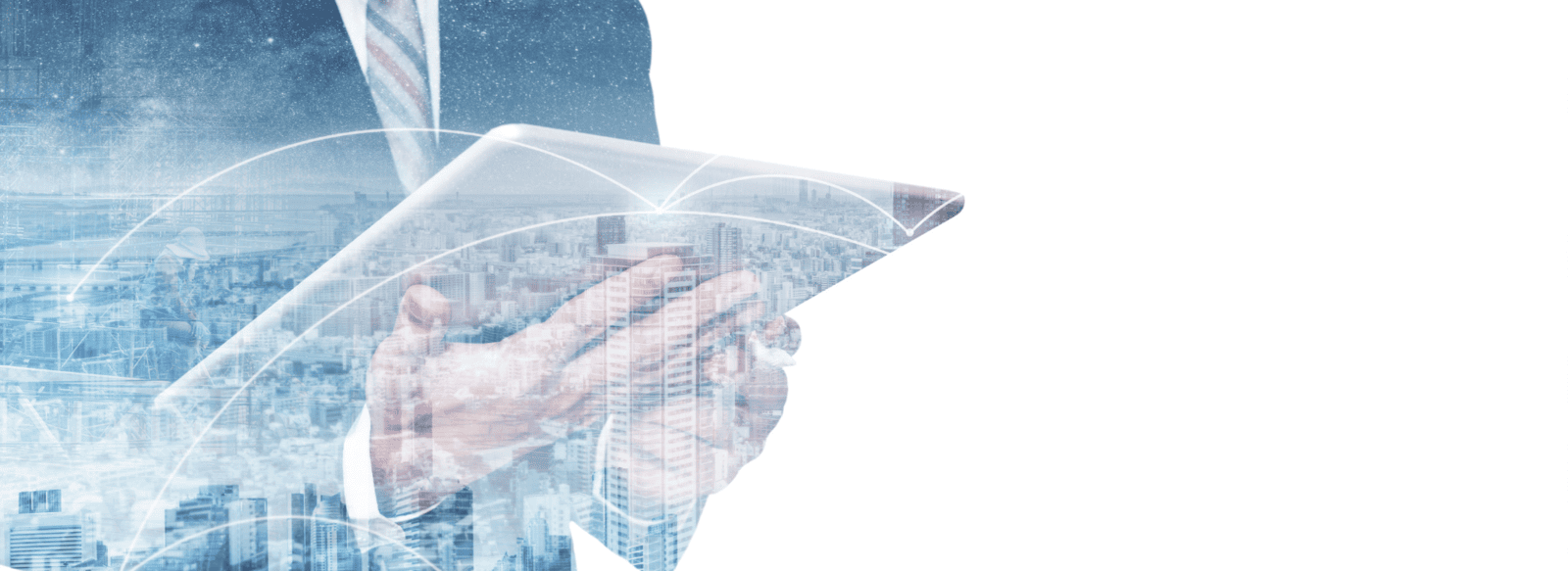
In the pursuit of operational efficiency and continuous improvement, the Day-by-Hour Report is a vital tool for Lean organizations.
By breaking daily production goals into manageable hourly targets, this report allows for real-time tracking, early identification of issues, and immediate corrective actions. Implementing the Day-by-Hour Report effectively bridges the gap between planning and execution, ensuring teams consistently meet customer demand.
This article serves as a detailed, step-by-step guide to implementing the Day-by-Hour Report within your production environment, driving transparency, accountability, and continuous improvement.
Step 1: Understand the Day-by-Hour Report
Step 1: Understand the Day-by-Hour Report
1.1 What Is It?
A real-time production management tool that tracks hourly performance against targets, highlights deviations, and facilitates immediate corrective actions.
1.2 Why It Matters
- Aligns production with takt time.
- Provides real-time performance monitoring.
- Facilitates proactive corrective actions.
- Encourages ownership and accountability.
Step 2: Design the Report Format
Step 2: Design the Report Format
2.1 Choose Report Type
The report can be physical or digital, depending on organizational needs and infrastructure.
Physical Reports
- Use whiteboards with clearly defined columns:
- Hourly Targets
- Actual Output
- Deviation (if any)
- Root Cause
- Corrective Action
- Cumulative Totals
- Place in visible areas for easy team access.
Digital Reports
- Integrate the report into existing ERP systems or production management software for automatic tracking.
- Use dashboards for real-time updates, accessible to operators and supervisors.
2.2 Key Report Components
- Planned Output: Hourly production goals.
- Actual Output: Recorded hourly performance.
- Deviations: Discrepancies between planned and actual output.
- Root Causes: Identified reasons for deviations.
- Corrective Actions: Immediate interventions and resolutions.
- Cumulative Totals: Running totals for the day.
Step 3: Prepare for Implementation
Step 3: Prepare for Implementation
3.1 Leadership Buy-In
Ensure leadership understands the value of the Day-by-Hour Report:
- Communicate expected benefits like increased visibility, reduced waste, and improved efficiency.
- Assign supervisors to lead implementation and monitoring.
3.2 Design and Standardize Training
Initial Team Training
Conduct sessions to educate operators, team leads, and supervisors on:
- Purpose and benefits of the Day-by-Hour Report.
- How to record hourly output, root causes, and corrective actions.
- Problem-solving techniques like 5 Whys and root cause analysis.
Ongoing Training
Provide regular refreshers to ensure team members fully understand and sustain the process.
3.3 Prepare Tools
- Set up whiteboards or configure digital dashboards.
- Define standard operating procedures (SOPs) for data collection, reporting, and review.
- Integrate tools with existing ERP systems if using digital formats.
Step 4: Implement the Day-by-Hour Report
Step 4: Implement the Day-by-Hour Report
4.1 Before the Shift
- Review Targets: Supervisors meet teams to communicate daily goals.
- Ensure Preparedness: Confirm tools, materials, and machines are ready.
- Assign Responsibility: Allocate hourly targets to operators or workstations.
4.2 During the Shift
- Hourly Recording: Operators record output at the end of each hour.
- Identify Deviations: Immediately flag discrepancies and note root causes (e.g., equipment failure, material delays).
- Take Corrective Actions: Supervisors collaborate with teams to resolve issues, such as:
- Adjusting resource allocation.
- Conducting minor maintenance.
- Ensuring timely material flow.
- Document Actions: Log root causes and corrective actions for future analysis.
4.3 Supervisors’ Gemba Walks
Supervisors perform Gemba walks to:
- Observe real-time production activity.
- Engage with operators to understand challenges.
- Validate the accuracy of recorded data.
- Verify the execution of corrective actions.
Step 5: End-of-Shift Reviews and Analysis
Step 5: End-of-Shift Reviews and Analysis
5.1 Team Review Meeting
Conduct a brief end-of-shift huddle to:
- Review overall performance against targets.
- Discuss major deviations and corrective actions taken.
- Celebrate achievements to encourage team engagement.
5.2 Supervisor Analysis
Supervisors analyze the completed Day-by-Hour Report to identify trends:
- Recurrent deviations or bottlenecks.
- Machines or processes causing regular disruptions.
- Opportunities for operator training or process improvements.
5.3 Use Data for Continuous Improvement
Share insights with leadership to:
- Plan long-term solutions to recurring issues.
- Optimize resource allocation for future shifts.
- Initiate Kaizen events to drive continuous improvement.
Step 6: Sustain and Optimize the Process
Step 6: Sustain and Optimize the Process
6.1 Regular Gemba Walk Reviews
Supervisors and managers must:
- Conduct daily Gemba walks to observe processes and engage operators.
- Reinforce accountability and ownership of output targets.
- Review corrective actions and ensure their effectiveness.
6.2 Continuous Improvement Culture
Promote a culture of improvement through:
- Regular team brainstorming sessions.
- Encouraging teams to identify waste and propose solutions.
- Recognizing and rewarding improvement suggestions.
6.3 Periodic Training and Feedback
- Conduct monthly or quarterly training sessions to address gaps in understanding.
- Review feedback from teams to refine the Day-by-Hour Report process.
6.4 Integrate with Lean Tools
Combine the Day-by-Hour Report with:
- 5S practices for organized workstations.
- Kanban systems to optimize material flow.
- Root Cause Analysis tools to address recurring deviations.
Step 7: Leverage Technology for Integration
Step 7: Leverage Technology for Integration
7.1 ERP Integration
For digital adoption:
- Integrate the Day-by-Hour Report into ERP systems for automated tracking and real-time visibility.
- Link machine outputs to dashboards to minimize manual logging.
- Provide supervisors and teams with mobile access to the dashboards for on-the-go updates.
7.2 Continuous Data Analysis
Leverage digital reports to analyze:
- Hourly trends over days, weeks, or months.
- Root causes of inefficiencies using visual tools like Pareto charts.
- Performance gaps to plan strategic improvements.
Conclusion
Conclusion
Implementing the Day-by-Hour Report through this structured approach ensures transparency, accountability, and continuous improvement. By integrating Gemba walks, corrective actions, standardized training, and both physical and digital reporting formats, organizations can monitor performance in real-time and address inefficiencies immediately.
Supervisors play a pivotal role in reinforcing the process through daily Gemba walks and performance reviews. When integrated with ERP systems and Lean tools, the Day-by-Hour Report becomes an essential mechanism for achieving operational excellence.